Grouting Procedure
When directional drilling, the normal procedure is to bore a hole that is roughly 30% bigger than the size of the pipe that is being installed, this is to help with the integrity of the pipe and the installation process.
Once the pipe is installed, there can be an area around the pipe that can be an open space called an (Annulus) this area can be filled up with the grouting procedure. Depending on the ground condition and drill hole slope, there are different ways in witch we can apply this grout.
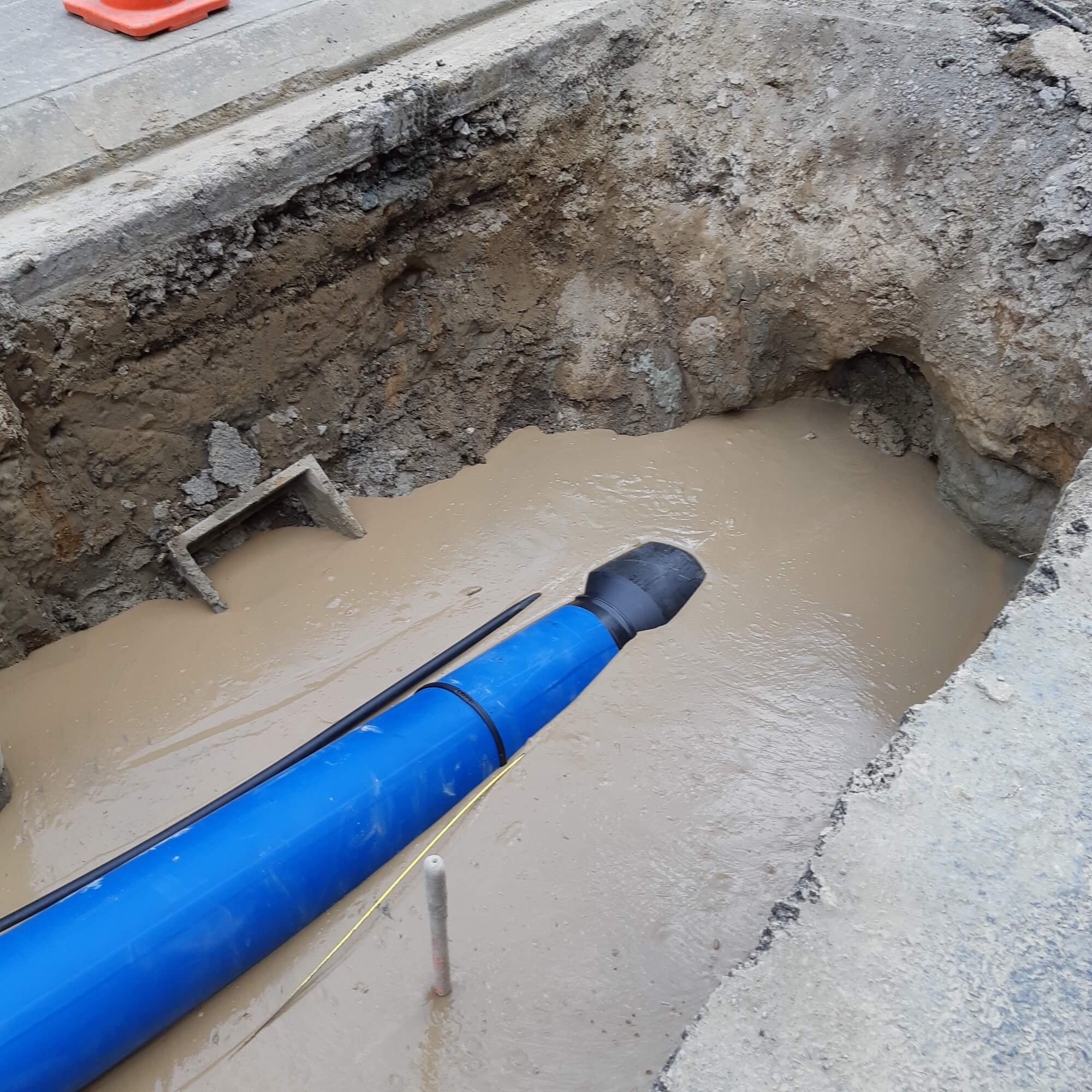
MAC Civil Construction created a grout plug that is used when drilling on hills or the drill hole is on at least a 8 degree slope, this is welded on the string and pulled up into the drill hole, which plugs the hole and stops any grout from leaving the drill hole.
The 40mm pipe is one of the ways in with we grout, this pipe has holes in it every 3m at the rear half of the pipe only, so that the grout fills up to the plug first and then comes out towards the drill.
Grouting is ideal for protecting the product from volcanic ground conditions, which are known in the New Zealand region. In this situation we would bore a hole that is 60%, that of the pipe installed, install a grout plug and fill that area with a specialised grout that protects the pipe from the earths elements. (Engineer to advise if they want this applied)
Grouting is mainly used to avoid any kind of underground stream and eventually cutting a bigger area out underground due to the flow of water.